Phillip Island Project In Hia Housing Magazine
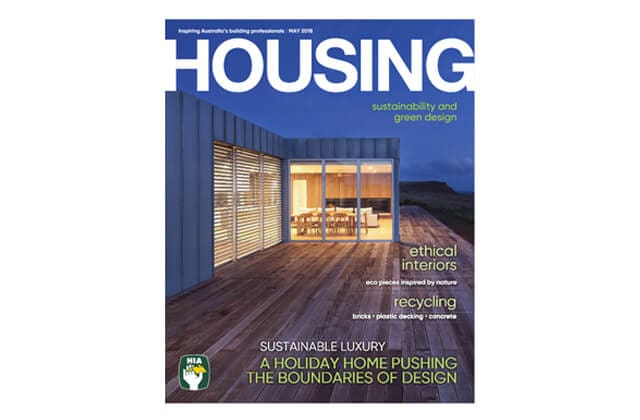
Words from HIA Housing Magazine – www.hia.com.au
Settled unobtrusively on a wild shoreline of Victoria’s Phillip Island, this effortlessly beautiful holiday home evokes the nostalgic charm of Australia’s iconic beachside cottages; with their spare mid-century styling and perennially sandy floors. At the same time, its progressive design and 21st century sensibilities herald a bold new take on contemporary architectural ingenuity.
The home is constructed – quite simply – from seven prefabricated modular units, assembled into two rectangular forms and anchored to the landscape by an expanse of raw timber decking. Extensive glazing along the front of the structure brings the spectacular ocean views into almost every part of the home, and, from the outside, shimmers with the reflection of the waves. The interiors, pared back to match the stark lines of the exterior, are serene, spacious and airy.
But there’s more to this four-bedroom, 300-square metre holiday house than clean lines and endless ocean views. It’s a high-performance, sustainable home, designed and built by modular construction pioneer and decade-long HIA member Modscape. This unique company was established in 2006 by a group of shareholders who value design, innovation and sustainability. ‘Modscape designs and builds beautiful and functional modular homes and commercial projects across a range of industries – from healthcare and education to hospitality and transport,’ says managing director Jan Gyrn.
The company’s innovative approach to building, where the majority of construction work is carried out inside its Melbourne factory, delivers a range of advantages: ‘We view prefabrication as the ultimate means of construction for sustainable homes because we have more control building it in one location, there is less waste and no commuting back and forth to the site,’ Jan explains. Weather delays and unforeseen complications are virtually eliminated, which means projects can be delivered on predictable timelines and for a fixed cost.
For the Phillip Island project, Modscape’s clients were seeking a quiet sanctuary from the bustle and stress of city life. Jan says that while this imperative certainly informed the design process, the structure was also shaped in direct response to both the beauty and climatic extremes of its windswept coastal location. ‘Important to the design was the organisation of internal and external living spaces to ensure they provide shelter at different times of the day and year, while still allowing the amazing views to be experienced from within,’ he explains. ‘[The finished home] successfully allows the epic coastal location to be experienced in all its many states.’
The glass-clad, seaward-facing western elevation of the main house module takes the brunt of the weather, and large sections of glazing to the northern walls bring winter sunlight into the living spaces. To the rear, a second module, shielded from the high winds, incorporates the garage and entryway, as well as an enclosed courtyard and pool area.
The seamless transitioning between indoors and out is one of the home’s primary functions, and underpins the building’s connection to the natural landscape. This is enabled by the full-height glass doors spanning the entre width of the home’s central living and kitchen area, which open onto the deck and the 180-degree views.
Internally, the 6-star rated home is impervious to external temperature extremes, thanks to the integrity of Modscape’s construction methodologies: ‘All of our eco-friendly homes are based on sustainable design principles that minimise environmental impact, maximise year round comfort and reduce running costs,’ Jan says. ‘The modules are made from fully-welded structural steel frames with Structural Insulated Panels (SIPs) used in the walls, ceiling and floor. The SIPs generate a thermal property that makes them an ideal choice for extreme climatic conditions.’
In this instance, the site was also carefully analysed for effective orientation (whilst maximising on the view), and passive heating and cooling was optimised using selective window placement to encourage cross-breezes and ventilation, double glazing and climate-appropriate insulation. A Heatmaster open fireplace and Haiku ceiling fans are the only additional heating and cooling systems required. The home isn’t connected to town water, which necessitated the inclusion of an underground 80,000-litre water tank.
The raw beauty of the site, and its proximity to the ocean, called for particular consideration of the home’s external form. ‘With such an epic location it was important that the home did not compete with the landscape,’ Jan says. The front, ocean-facing module of the house was clad in zinc, which delivers extreme durability along with a certain visual softness. ‘It is not hard to fall in love with zinc thanks to its amazing environmental properties, its unique and luxurious aesthetic appeal and its flexible, durable and efficient performance,’ Jan says.
The rear section is clad in beautifully understated vertical shiplap Pacific Teak boards. The timber was chosen for its warmer hues that will compliment the zinc as it continues to weather. ‘The materials selected and the building’s form sits as part of the environment, so landscape and architecture are connected.’
Amazingly, the entire structure was built inside Modscape’s factory in just 12 weeks. The controlled factory environment ensured a high level of quality control was maintained and less time was spent on site,’ Jan says. The home craned onto site in one day, and services were connected over the next fortnight. ‘A few short weeks later, the clients were enjoying the summer break from their new holiday home.’
Words from HIA Housing Magazine – www.hia.com.au
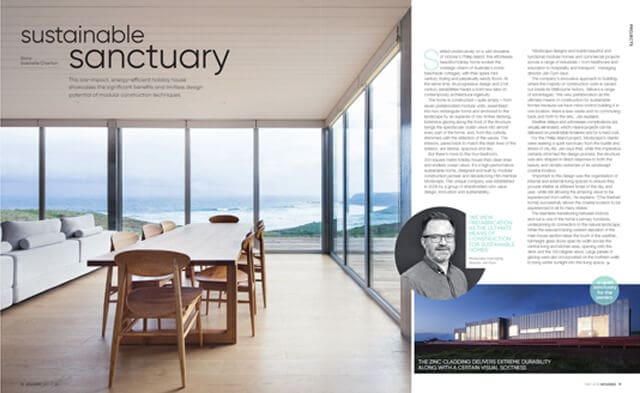