OFF-SITE CONSTRUCTION – BENEFITS FOR THE HEALTHCARE INDUSTRY
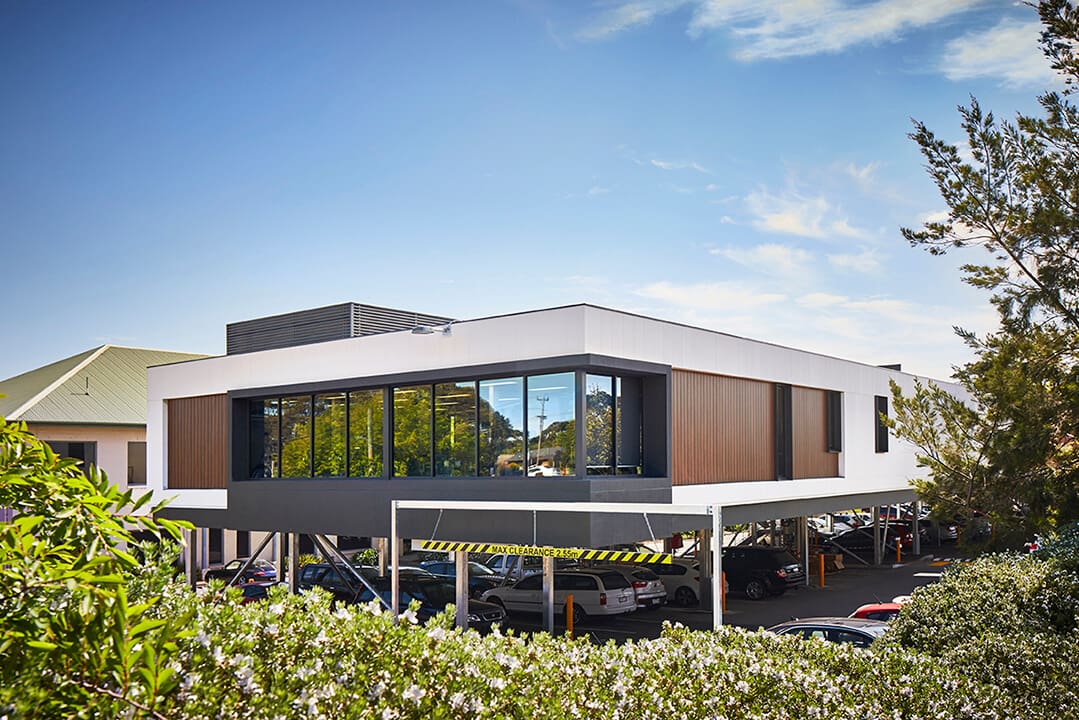
Recently the NSW Government announced a welcomed $2.3 billion budget boost for hospitals and health services. As part of the increase, the state government will invest in extra frontline clinical and support staff in addition to the construction of 40 new facilities, upgrades and redevelopments.
To meet the demand in a timely, efficient and high quality manner, smart developers and contractors will turn to modular construction systems and techniques.
Off-site modular construction systems and techniques come with a host of benefits for the healthcare industry, including:
- Less disruption to staff, patients and local residents
- Less noise and on-site waste
- Stringent quality controls ensuring consistency through the entire project
- No weather, trade or supply issues
- A fixed timeline for design, construction and delivery
- A more rapid build time
- Budget certainty
The methodology of prefabricated construction has been around for decades and integrating modular elements into construction is not a new strategy. The likes of Lendlease, Mirvac and Ramsay Healthcare are already realising the benefits of modular across numerous projects and industries. And a range of canny investors are well versed in factoring in significant time savings to project feasibilities by using modular construction.
Modscape has constructed a range of innovative modular hospitals and modular medical buildings across Australia:
The Avenue Private Hospital
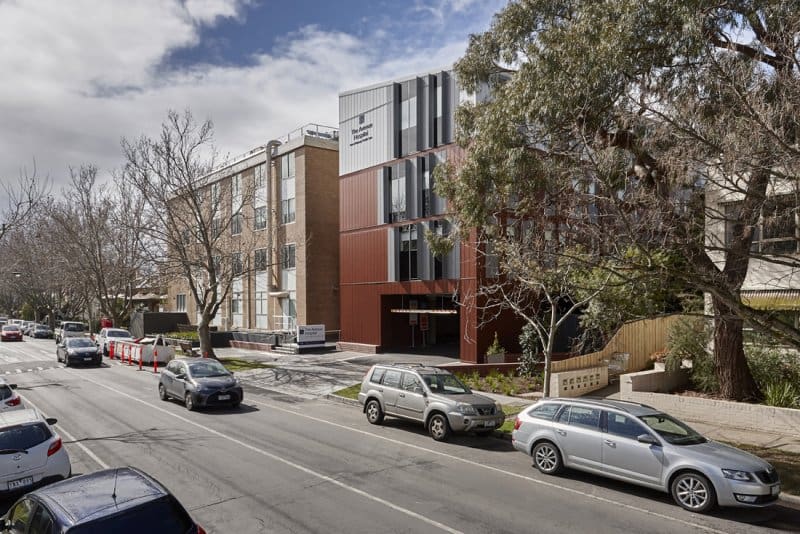
Modscape was engaged by Ramsay Healthcare to develop a modular solution for The Avenue Private Hospital. Modular construction enabled them to quickly meet the hospital’s increasing accommodation demands with the 36 modules over four levels installed in just two days to keep disruption to a minimum. The modules were delivered with a complete façade and structural system. Following installation, concrete floors were poured into each level, ready for the fit-out of operating theatres. The off-site construction of the modules contributed to a heavily reduced project delivery timeframe.
Waverley Private Hospital
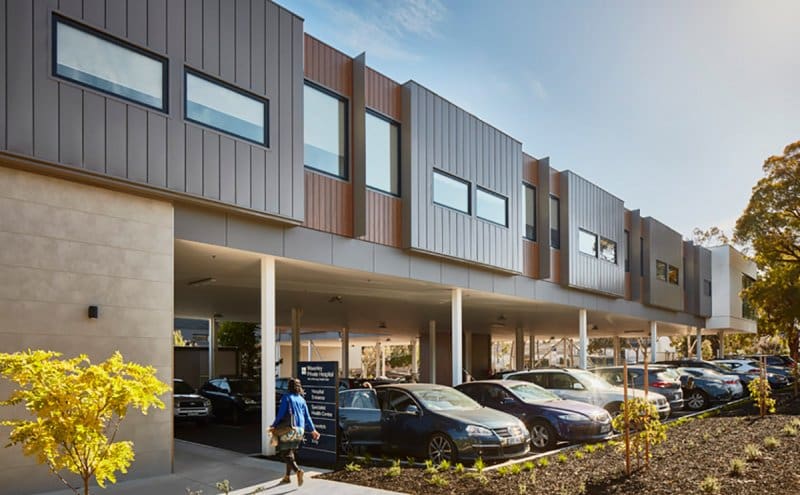
Similarly Modscape’s modular construction techniques were employed at Waverley Private Hospital to help the Ramsay Healthcare meet their increasing accommodation demands while minimising onsite disruption. The addition of 32 new private rooms for the hospital’s surgical ward were constructed in 16 weeks. The modular addition compliments the existing hospital facilities and floats above the existing carpark, which remained operational throughout the entire construction period.
Hornsby Hospital
A condensed project delivery time and the minimisation of site disruption are not the only motivation for using modular construction.
Health Infrastructure NSW adjusted their approach in order to achieve better short-term and long-term results in the Hornsby Hospital refurbishment project. Working alongside Richard Crookes Construction, Modscape constructed additional ward rooms as a temporary solution while the refurbishment of the existing facility is undertaken. The modular addition was constructed in 11 weeks within Modscape’s factory and installed over two nights to minimise disruption to staff and patients. A further six weeks onsite saw the completion of final fitout works. Once the five year refurbishment project is complete, the modules will be relocated to a different area where they will become part of the permanent facility.
To stay at the forefront of healthcare design, relevant to patients needs and to meet the demand in a timely, efficient and high quality manner, savvy healthcare providers, developers and contractors are using modular construction to their advantage.
For more information about how we can assist with your modular hospital build, please contact us.
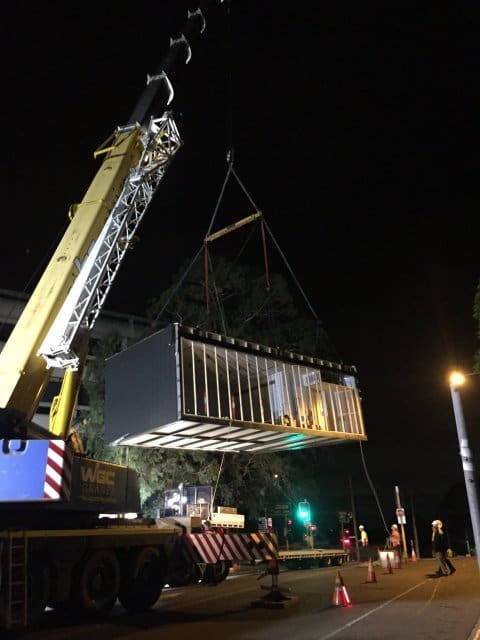